課題
工場の生産過程において、各工程の作業実績が曖昧で、リアルタイムでの進捗状況を把握できず、情報が正確に提供されていませんでした。さらに、目視や手記入、手入力による作業は時間とコストがかかり、ヒューマンエラーが発生しやすい状況でした。このため、生産計画を正確に立案するには高い熟練度が必要であり、生産の効率化が課題となっていました。
提案
無線端末とバーコード入力方式を採用し、リアルタイムで各工程の進捗状況を正確に把握できるシステムを提案しました。このシステムにより、作業者の負担を軽減し、ヒューマンエラーを削減します。また、リアルタイムでの進捗管理により、リードタイムの短縮や無駄の排除が可能となり、生産計画の効率化と在庫の圧縮を実現することを目指しました。さらに、既存の運用方法に対応できる柔軟なシステム拡張も提供しました。
解決⽅法
バーコード入力方式と無線端末を活用して、各工程での進捗状況をリアルタイムに記録・管理する機能を実装しました。これにより、作業者が簡単かつ正確に作業を行える環境を整備し、ヒューマンエラーを防止しました。リアルタイムでの進捗状況の把握により、無駄な工程が明確になり、リードタイムの短縮が可能となりました。また、正確な進捗情報を基に生産計画の立案が容易になり、在庫の適正化が実現しました。
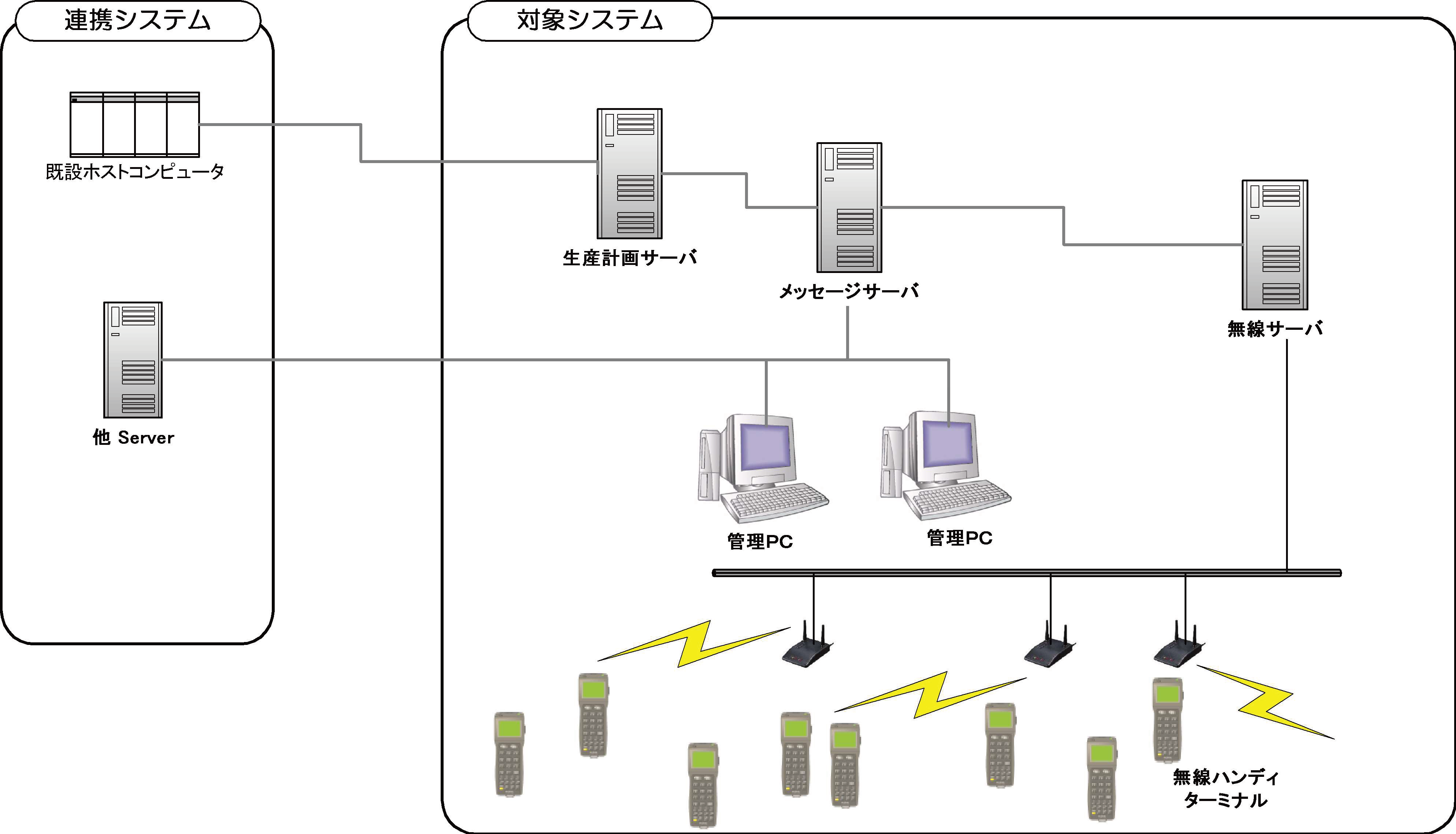
導⼊効果
システム導入後、各工程の進捗状況がリアルタイムで把握できるようになり、無駄な工程や作業が削減されました。これにより、リードタイムが短縮され、作業効率が飛躍的に向上しました。バーコード入力方式によってヒューマンエラーが減少し、作業者の負担も軽減されました。正確な進捗管理が可能となり、生産計画の精度が向上し、在庫の圧縮にも成功しました。
開発環境
・開発言語:VB、VC++
・データベース:PL/SQL、ORACLE
・通信技術:CORBA、ソケット通信
・ハードウェア:無線端末、ハンディターミナル